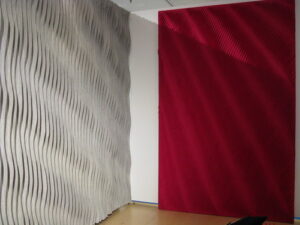
The beautiful thing with DIY projects is that you get to save a lot more than you think you’re actually saving, and it doesn’t end there. You also get to enjoy the satisfaction that comes from finishing such pet projects, as well as other bragging rights you might have with your friends and colleagues. Absorbing panels are very essential for studio and home soundproofing, and if you are looking at “How To Make Cheap Sound Absorbing Panels”, you are definitely in the right place.
For starters, you’ll have to:
- Get the right wood and cut them into your desired sizes.
- Build the frame.
- Get a durable absorbing material and fabric for the cover. Among several others.
To begin this project, you’ll need the following, especially if the size is a 2X4 inch panel. For other sizes, you’ll need to make the necessary modifications.
Contents
How To Make Cheap Sound Panels – DIY Guide
Tools needed
- A hand drill machine.
- Drill bits of different sizes, especially the smaller ones (you’ll need them for pilot holes).
- A measuring tape.
- A knife (serrated) or scissors.
- A gun (OH, I meant a staple gun. Sorry for getting your heart racing).
- Screwdriver cross-head drill bit to save time.
- A saw (I’ll recommend an electric saw, but if you can’t afford or borrow one, a manual saw will do).
- Work gloves and safety goggles for safety.
Materials needed
- Wood glue (not compulsory).
- 60-inch fabric (the fabric must be made of cotton, as they are good absorbers of sound).
- Cans of PBR (4X300 ml)
- A reasonable amount of staples.
- Wood screws having a dimension of 40X1.5 inches. 6 or more should do.
- Cheap options of Owens Corning 703 with a dimension of 2X2″X4X2″
- Wooden boards measuring 4X8’X4″X1″.
Step 1: Carefully cut the wood into parts
If you want to make things easy when cutting, ensure you get an 8ft board, especially if you are sticking with the 2″X4″ absorbing panel dimension.
Getting an 8ft board will simply require you to cut the board into two equal parts to get your desired dimension of 2″X4″. This board can be gotten from your local hardware store or you can simply place an order on Amazon.
Be mindful of the board quality and don’t be carried away by the cheap cost. Ensure the board in question is not bent but straight. If your hardware store gives you a free opportunity to cut the board, then by all means take it. But ensure the board is cut to the required length so you don’t have to repeat the process when you get home.
Step 2: Build the framework
You will be busy for the next hours or so, I suggest you get all your materials and tools close by, ensure your hand drill is properly configured, and if you are a music person, you may want to arrange a playlist of your favorite tracks or album on alexia or any other device you use. This journey promises to be an interesting one. I wouldn’t recommend you drink an intoxicated beer as you’ll be using power tools that need your 100% focus. Water should do.
Carefully arrange the wood close to the required dimensions, but place it to measure a total of 4′ instead of 4’2″ so it would be easier to place and trim your rock wool fabric when the time arises.
Get your drilling machine and drill at least two pilot holes on the bottom and top of the 4′ wood. While at it, ensure the hike is at least ½ inch from each other so that the screws have the required allowance to go into the one-inch boards.
I will suggest you add wood glue to the edges of the frame before driving in your screw. Not that it has any soundproofing effect, or the screws wouldn’t do a good-enough job. However, the glue acts like a two-step verification. They help to strengthen the hold. This should be done on all the corners of your frame.
Step 3: Reinforce the framework
The purpose of reinforcing the framework is to create a platform for installing the insulation and also improve the strength and durability of the overall framework. If you don’t, it wouldn’t last as it should, and would also be less effective.
To begin this process, place one of the 2′ wood in the middle of the already constructed frame, then measure 2′ at the panel’s top located at each of the longer sections of the framework to correctly reach the middle.
Use your hand drill to make a pilot hole measuring ½ inch in two places, and this should be located at the front of the framework so that your 2′ wood will sit properly. This should be done on both sides of the long wood so that your insulation material is properly aligned in the front of your panel. And just like before, I suggest you glue both ends before screwing to have the best result.
Optionally, you can choose to add small pieces of wood at the corners to help not only improve the sturdiness of the framework but also to provide more area for your insulation to sit perfectly. These cuts do not increase the weight of the framework, so you need not worry.
I’ll suggest you use a jigsaw or a circular saw if you don’t want to be stressed out. You can use any of the leftover wood and simply draw a right-angle triangle as a guide.
Once these triangles are ready, place them 2″ below what the panel can accommodate so your insulation can properly fit, then simply add wood glue and screw with a single screw for one corner each.
Step 4: Measure and cut out the insulation
Sorry if you feel stressed out by now, but I hope it has been worth it. Once refreshed, put in your work gloves, and let’s get it over with.
Get your rock wool material (Roxul in particular) having the dimension of 2’x4’x2″. You might also want to use the Owen Corning brand, depending on what you feel will work for you. However, in terms of cost, the Roxul brand is cheaper and does a very good job as the Owen Corning brand. The Roxul rock wool material is available on Amazon, and a box of 6 should work out perfectly for you.
With your frame standing at 2′, and your insulation at 2′ width, your insulation should perfectly fit into your framework. However, this might not be the case if you happen to have discrepancies in your measurements. If this is the case, you might want to use your serrated knife and make the necessary adjustments. If you aren’t sure where to trim, you might want to trim along the long side of the framework for the best result, but all this wouldn’t be necessary if your measurements are correct.
Remember to take into account the 2″ that was removed
at the beginning, so this might also mean you have to trim the insulation. Regardless of the decision you choose to take, ensure your insulation sits perfectly.
Step 5: Cover the frame with a fabric
When it comes to the surface fabric, you have to ensure it is breathable, as this means it wouldn’t reflect sound, which would defeat the purpose of everything.
You can test for this by placing the fabric over your nose. The more air you can breathe, the more suitable it is. Many people who have carried out this project have recommended the burlap material because of not just its soundproofing properties, but also the beauty it brings. It may come a bit pricey though as it costs around $20 per yard.
Try getting the 60′ fabric so it can fit into the framework you have already made. Use your purchased fabric and place it over the framework containing the installation. Ensure it is properly stretched out, so it can cover every area of the framework.
To avoid bubbles, staple the first side of the fabric to any part of the framework, then gently drag until you obtain a full stretch. Repeat this process until the entire surface is covered without bubbles or wrinkles.
As for the corners, there is no particular trick to them. Simply make it look neat as though you were wrapping a gift item. Then staple it when you are done.
You can choose to repeat the process for the back of the frame, but you don’t necessarily have to.
Also read: What materials absorb sound? The types and how they work
FAQs
What is the cheapest way to soundproof wall?
There are several cheap ways to soundproof a wall, but what’s important is that you make do with what you have. If this includes a bookshelf, you can simply place it on the wall where the noise is emanating from.
What cheap materials absorb sound?
Examples of cheap materials that absorb sound include egg cartons, green glue, rugs, etc.
What is the best absorber of sound?
The best absorber of sound you are likely to commonly find around is cotton. Cotton does a very good job of not just blocking sound but absorbing sound.
Conclusion– How to make cheap sound absorbing panels?
You tend to save a lot and also get to enjoy a hands-on experience with DIY tasks. Hopefully, this won’t be different. Kindly let me know if you have any questions or suggestions regarding the said topic, I’ll be in the comment section. Cheers.